We will upgrade the technology of automation equipment production in Korea through the development of high-function sensors and high-function controllers.
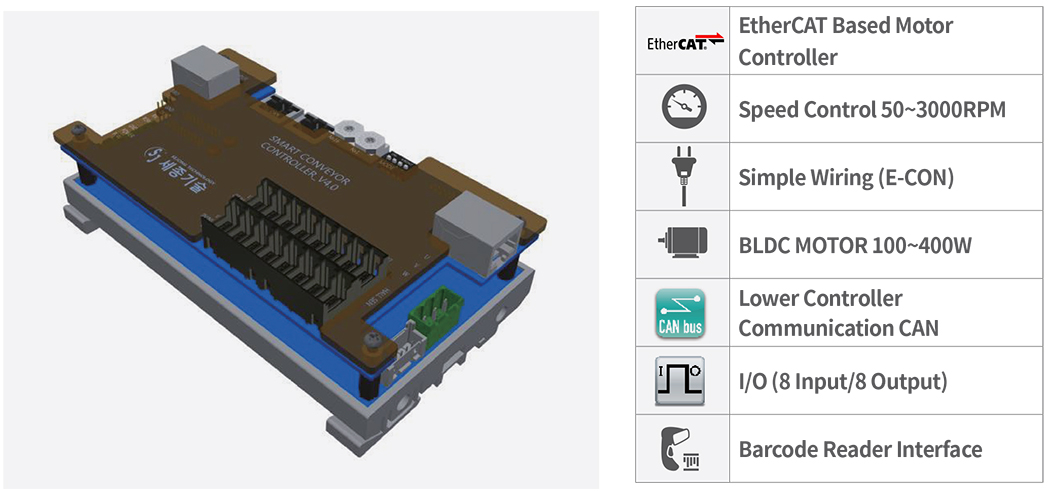
Feature
EtherCAT Based BLDC Motor Controller
Ethernet (100Mbps, Full - Duplex) based Fieldbus. EtherCAT supported BLDC motor driver built in controller. EtherCAT supports fast data transfer with device nearby and supports connection with various devices without topology limit.
Various Form of Conveyor Support
Supports various form of conveyor. User can control buffer/diverter/dispenser rotate conveyor/etc even without a program only by configuring DIP Switch.
BLDC Motor Driver
Controller has built-in BLDC motor driver which controls BLDC motor that is installed on conveyor. Available motors are 100-400W and it can control the speed by communication with higher EtherCAT.
Numerous Communication Feature
The controller supports numerous communication feature for sub controllers. Through CAN / RS232 communication, it can communicate with sub conveyor controller, extent IO board and BCR reader.
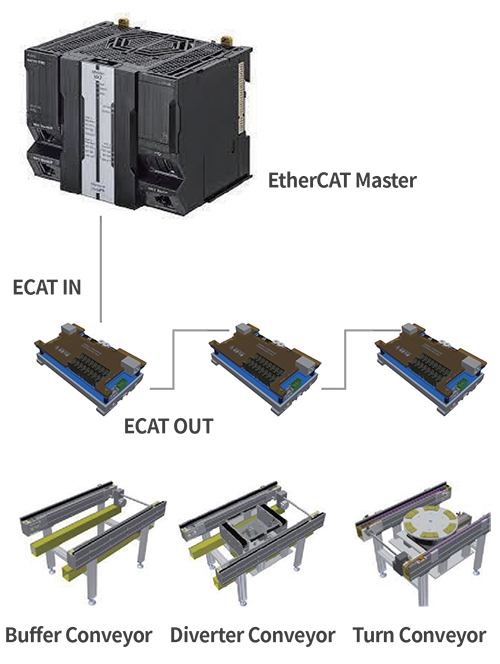
Specification
BLDC Motor Driver Spec
ModuleName | SATURN-SC-BLDC |
---|---|
Voltage Input | AC 90V~264V±10% |
Controller Voltage | 24VDC±10% |
Electricity Consumption | 300mA(I/O current exclude) max |
Control Type | 32bit ARM based control |
Rotate Speed | 0~3,000 rpm |
Protect Function | Overcurrent, Overheat, Overvoltage |
LED Indication | Power Status, Overcurrent Status, Overheat Status, Error Status |
I / O | 8 Fixed Input / 8 Fixed Output |
Usage Temp | 0~50℃ |
Usage Humidity | 30~85% RH (No Condensation) |
Store Temp | -20~70℃ |
Store Humidity | 10~90% RH (No Condensation) |
Vibration Resistance | 0.5G |
Ether CAT Spec
Communication Type | Ether CAT |
---|---|
Physical Layer | Ethernet - 100 BASE - TX |
Connector | RJ45 ECAT IN / ECAT OUT |
Topology | Line(When composed only of products) Tree, Star(When Junction Port Used) |
ECAT Device ID | With Hex Switch, Configured Station Alisa Configure 1- 255 |
Support Protocol | COE(CAN poen Application protocol over Ether CAT) |
Support Action Mode | Cyclic Synchronous Position (CSP Mode) |
External Measurement
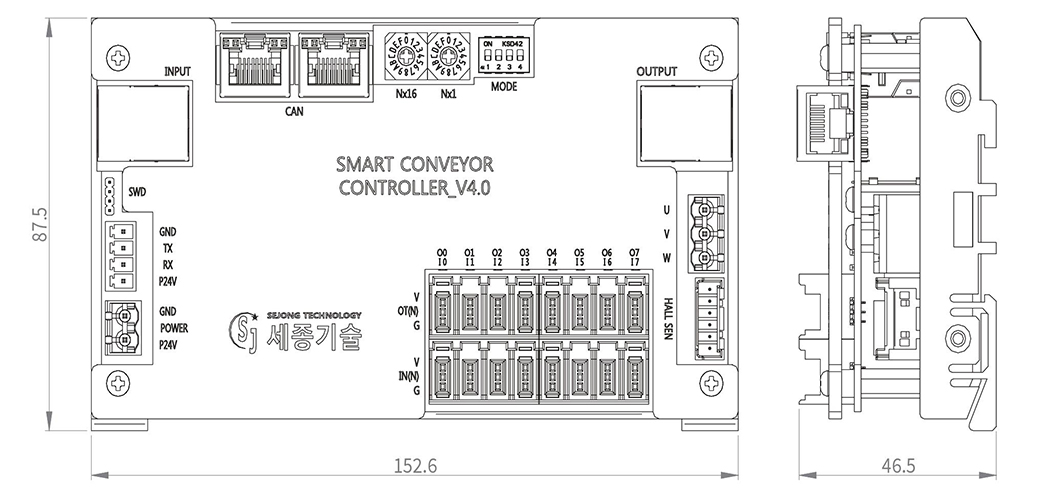
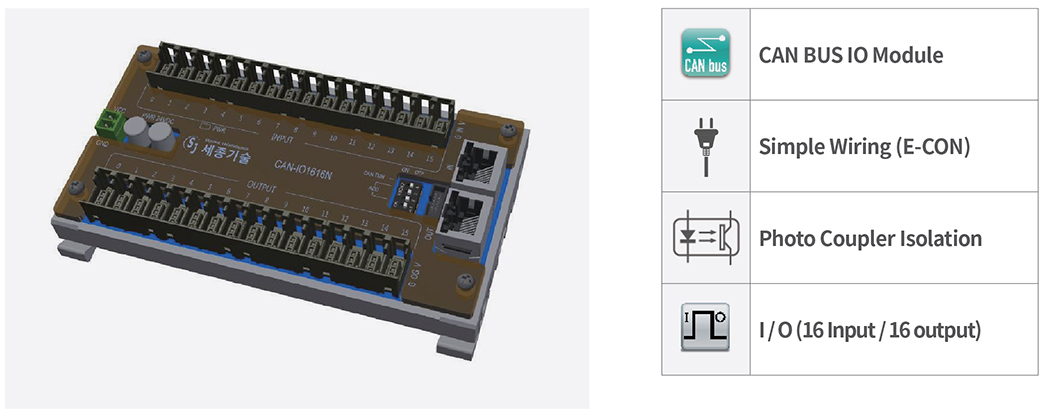
Feature
CAN Communication 16IN / 16OUT IO Module
CAN Communication supported IO Module. Supporting 16 Input channel/ 16 Output Channel. Input 16 Channel / Output 16 channel support. Master Controller / SATURN - SC - BLDC controller connection support
Easy Wiring
E-CON connector type can easily plug in/out. Two RJ45 Type connectors are provided making the communication easier to connect.
Photocoupler Isolation
I/O terminal is insulated with photocoupler making connection easy with no extra circuit.
Maximum 8 Connection
Configurable address through Dip Switch Up to 8 I/O board can be used simultaneously.
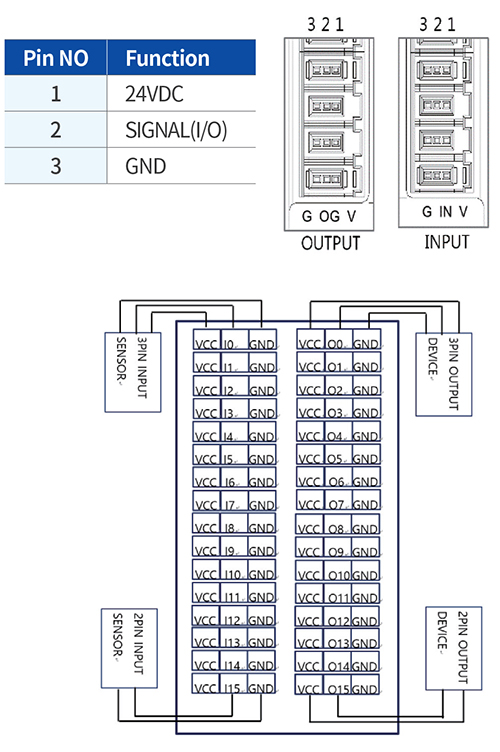
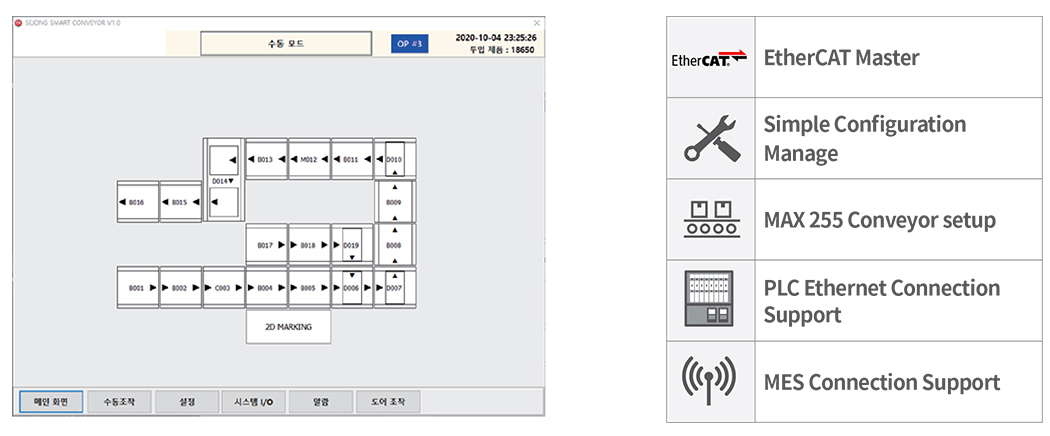
Feature
EtherCAT Master Controller
Linux based OS is used. Built-in EtherCAT Master Protocol Stack and able to control up to 255 conveyor
Converyor Setup without program
Able to run without program after configuring the system. Setup program can manually control and check I/O status. Conveyor motor drive speed and acc/deceleration speed can be set with parameter configuration.
Mitsubishi PLC Communication Support
Mitsubishi MC protocol supported, letting upper/lower system get same data as Mitsubishi PLC.
MES TCP / IP Communication
MES connection function by TCP/IP communication. Protocols may be developed by customer requirement.
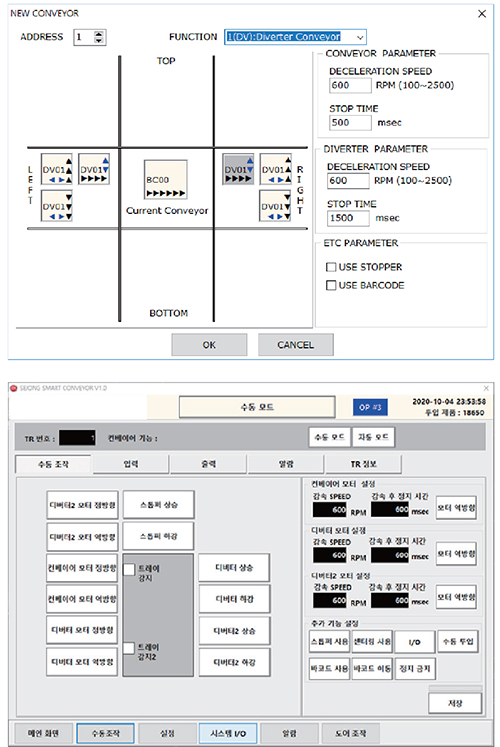